Mastering Warehouse Management: Proven Strategies for Optimal Productivity
Jan 02, 2020
Are you ready to take your warehouse management skills to the next level? In today's fast-paced business world, mastering efficient and effective warehouse operations is crucial for maximizing productivity and staying ahead of the competition. Whether you run a small warehouse or manage a large distribution center, implementing proven strategies is key to streamlining processes, reducing costs, and improving overall efficiency. In this guide, we will explore the best practices and techniques that successful warehouse managers utilize to optimize their operations and achieve optimal productivity. From inventory management and layout design to implementing technology solutions, we will cover all the essential aspects that will help you unlock the full potential of your warehouse. Get ready to revolutionize your warehouse management and pave the way for increased profitability and success. Let's dive in!
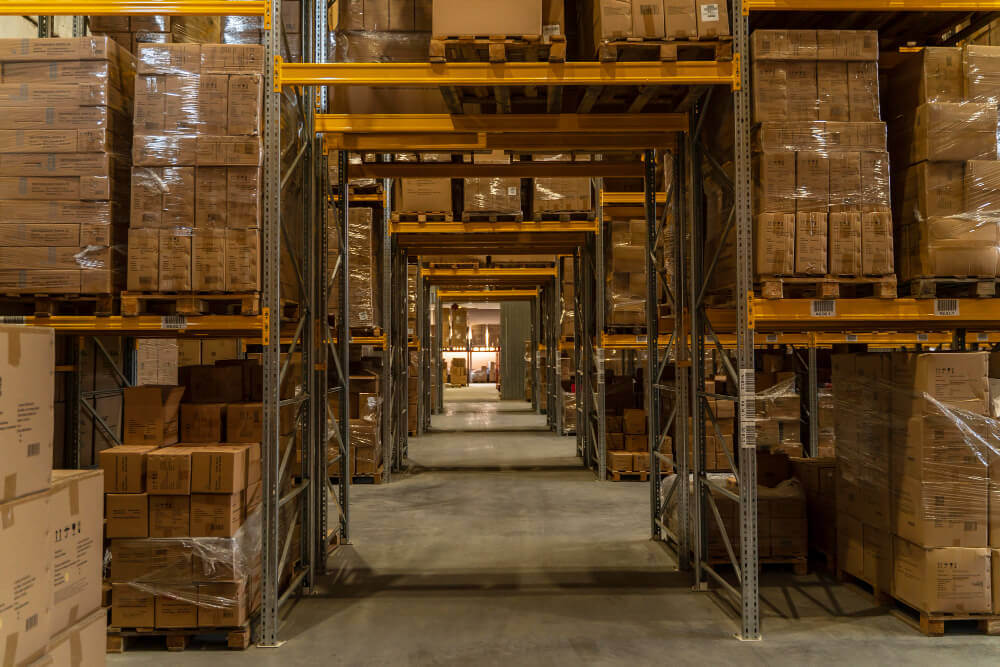
The Importance of Efficient Warehouse Management
Efficient warehouse management is the backbone of any successful operation. It ensures that products are stored, organized, and delivered in a timely manner, leading to improved customer satisfaction and increased revenue. Without proper management, warehouses can become chaotic and inefficient, resulting in lost inventory, wasted time, and unnecessary expenses. By implementing effective strategies, warehouse managers can optimize their operations, minimize errors, and maximize productivity.
One of the key benefits of efficient warehouse management is improved inventory control. By having a clear understanding of what products are in stock, where they are located, and when they need to be replenished, warehouse managers can avoid stockouts and overstock situations. This not only reduces carrying costs but also minimizes the risk of lost sales and dissatisfied customers. Additionally, efficient warehouse management allows for better utilization of available space, leading to increased storage capacity and reduced storage costs.
To achieve efficient warehouse management, it is essential to establish standardized processes and workflows. This includes defining clear roles and responsibilities, implementing effective communication channels, and establishing performance metrics to monitor and evaluate the efficiency of warehouse operations. By continuously analyzing and improving these processes, warehouse managers can identify bottlenecks, eliminate waste, and optimize the overall flow of goods in and out of the warehouse.
Efficient warehouse management is not just about improving internal processes; it also involves establishing strong relationships with suppliers and customers. By collaborating closely with suppliers, warehouse managers can ensure timely deliveries and maintain optimal inventory levels. On the other hand, by providing accurate and timely information to customers, warehouse managers can enhance transparency and build trust, leading to increased customer loyalty and repeat business.
In summary, efficient warehouse management is vital for optimizing productivity, reducing costs, and improving overall customer satisfaction. By implementing proven strategies and techniques, warehouse managers can streamline processes, minimize errors, and maximize the potential of their warehouses.
Key Challenges in Warehouse Management
While efficient warehouse management offers numerous benefits, it also comes with its fair share of challenges. Understanding and addressing these challenges is crucial for overcoming obstacles and ensuring smooth operations. Let's take a closer look at some of the key challenges faced by warehouse managers:
1. Inventory Accuracy: Maintaining accurate inventory records is a constant challenge for warehouse managers. Inaccurate inventory data can lead to stockouts, overstock situations, and customer dissatisfaction. Implementing robust inventory management systems and conducting regular cycle counts can help improve accuracy and minimize discrepancies.
2. Labor Management: Managing a diverse workforce with varying skill sets and availability can be a challenge. Warehouse managers need to ensure that they have the right number of employees with the necessary skills to handle daily operations. Effective labor planning, training programs, and performance management systems can help address this challenge.
3. Seasonal Demand: Many warehouses experience fluctuations in demand throughout the year. This can pose challenges in terms of staffing, inventory planning, and order fulfillment. Warehouse managers need to anticipate and prepare for seasonal demand by adjusting staffing levels, increasing storage capacity, and implementing flexible workflows.
4. Technology Integration: The rapid advancement of technology has brought about numerous opportunities for warehouse optimization. However, integrating new technologies into existing warehouse systems can be a complex and challenging process. Warehouse managers need to carefully evaluate technology solutions, ensure compatibility with existing systems, and provide adequate training to employees.
5. Supply Chain Complexity: As supply chains become more global and complex, warehouse managers face challenges in coordinating inbound and outbound logistics. Ensuring timely deliveries, managing customs and regulatory requirements, and optimizing transportation routes are just a few of the challenges that warehouse managers need to navigate.
By recognizing and addressing these challenges, warehouse managers can implement strategies and solutions that enhance efficiency and productivity. It is essential to stay updated with industry trends, continuously evaluate existing processes, and embrace technology advancements to overcome these challenges effectively.
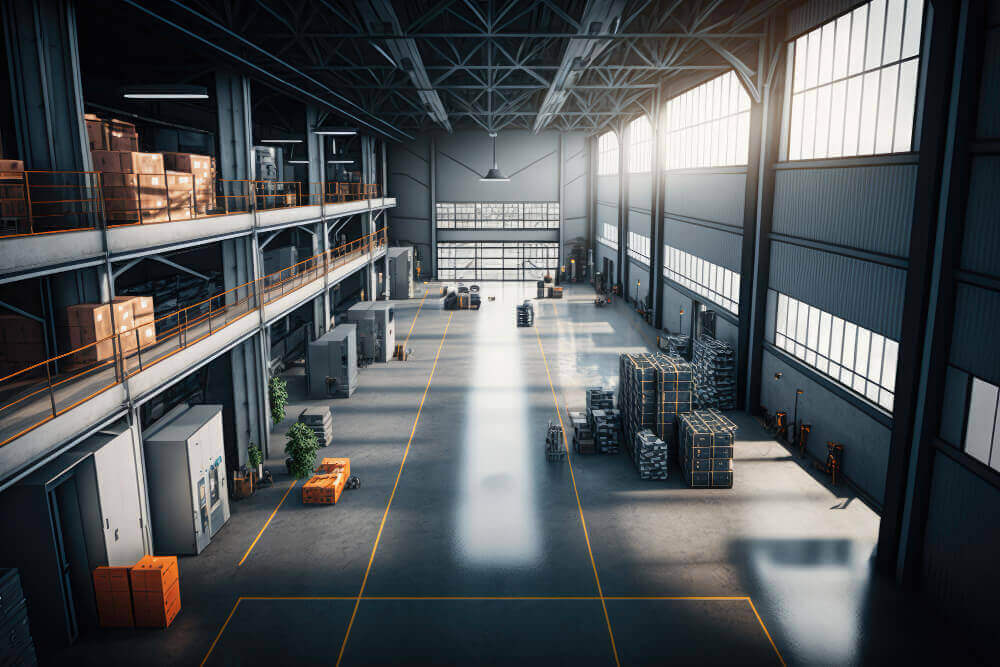
Warehouse Layout and Organization
The layout and organization of a warehouse play a critical role in optimizing operations and maximizing productivity. A well-designed warehouse layout ensures efficient movement of goods, minimizes unnecessary travel time, and enhances worker safety. Here are some key considerations for warehouse layout and organization:
1. Optimal Space Utilization: Effective space utilization is essential for maximizing storage capacity and minimizing costs. Warehouse managers should carefully plan the placement of racks, shelves, and storage systems to make the most efficient use of available space. Utilizing vertical space through mezzanines and high-rise storage systems can significantly increase storage capacity.
2. Logical Flow: A well-designed warehouse layout ensures a logical flow of goods from receiving to storage to order fulfillment. The layout should facilitate smooth movement of products, minimize cross-traffic, and eliminate bottlenecks. Warehouse managers should consider factors such as product velocity, order picking frequency, and order consolidation points when designing the layout.
3. Zoning and Segmentation: Warehouse segmentation involves dividing the warehouse into zones based on product characteristics, order types, or customer requirements. This allows for better organization, easier navigation, and faster order fulfillment. Warehouse managers should carefully define and label different zones, ensuring that products are stored in their designated areas.
4. Safety and Ergonomics: Worker safety should be a top priority when designing warehouse layouts. Warehouse managers should ensure clear pathways, adequate lighting, and proper ventilation. Additionally, ergonomic considerations such as workstation design, equipment placement, and proper lifting techniques should be incorporated to minimize the risk of injuries and improve worker productivity.
5. Flexibility and Scalability: The warehouse layout should be designed with future growth and changes in mind. Flexibility and scalability are key to adapting to evolving business needs. Warehouse managers should consider modular storage systems, adjustable racking, and flexible picking zones to accommodate changes in product mix, order volume, and customer requirements.
By carefully analyzing the specific needs of the warehouse and implementing a well-thought-out layout, warehouse managers can create an environment that promotes efficiency, productivity, and safety.
Get In Touch
Text usWarehouse Technology and Automation
In today's digital age, technology plays a crucial role in optimizing warehouse operations and driving productivity. By embracing warehouse technology and automation, warehouse managers can streamline processes, reduce errors, and enhance overall efficiency. Here are some key technologies and automation solutions that can revolutionize warehouse management:
1. Warehouse Management Systems (WMS): WMS software provides real-time visibility and control over warehouse operations. It enables warehouse managers to efficiently manage inventory, track orders, optimize picking routes, and generate accurate reports. WMS solutions can be customized to meet the specific needs of the warehouse, integrating with other systems such as Enterprise Resource Planning (ERP) software.
2. Barcode and RFID Technology: Barcoding and RFID (Radio-Frequency Identification) technology are widely used for inventory tracking and management. Barcodes and RFID tags can be attached to products, pallets, or storage locations, allowing for accurate and efficient data capture. Warehouse managers can use handheld scanners or fixed RFID readers to track inventory movement, monitor stock levels, and automate order fulfillment processes.
3. Automated Storage and Retrieval Systems (AS/RS): AS/RS systems automate the storage and retrieval of products, minimizing manual intervention and reducing the risk of errors. These systems use automated cranes, conveyors, and robotic shuttles to move products to and from designated storage locations. AS/RS solutions are particularly beneficial for high-density storage, fast-moving items, and facilities with limited space.
4. Pick-to-Light and Put-to-Light Systems: Pick-to-Light and Put-to-Light systems use visual indicators such as lights or displays to guide warehouse staff in picking or putting away items. These systems eliminate the need for paper-based picking lists or manual data entry, reducing errors and improving order accuracy. Pick-to-Light and Put-to-Light systems can be integrated with WMS software for seamless operation.
5. Voice-Activated Technology: Voice-activated technology enables warehouse staff to receive instructions and provide real-time updates using voice commands. This hands-free solution improves worker productivity and accuracy, as it eliminates the need for manual data entry or handling of paper documents. Voice-activated technology can be integrated with WMS or other systems for optimal efficiency.
6. Robotics and Automation: Robotics and automation solutions are increasingly being adopted in warehouses to handle repetitive tasks, such as picking, packing, and sorting. Warehouse robots can work alongside human employees, performing tasks with speed and precision. These solutions not only increase productivity but also enhance worker safety by eliminating strenuous or hazardous activities.
By leveraging these technologies and automation solutions, warehouse managers can optimize processes, reduce labor costs, and improve overall operational efficiency. However, it is important to carefully evaluate the specific needs of the warehouse and choose solutions that align with the organization's goals and resources.
Best Practices for Warehouse Operations
Successful warehouse managers embrace a set of best practices to optimize operations, maximize productivity, and ensure a smooth workflow. These best practices focus on efficiency, accuracy, safety, and continuous improvement. Here are some essential best practices for warehouse operations:
1. Standardized Processes: Establishing standardized processes and workflows is essential for consistency and efficiency. Warehouse managers should document and communicate standard operating procedures (SOPs) to ensure that all employees follow best practices. Regular training and performance monitoring can help reinforce these processes.
2. Continuous Process Improvement: Warehouse managers should continuously analyze and improve processes to eliminate waste, streamline operations, and enhance productivity. Methods such as Lean Six Sigma can be used to identify bottlenecks, reduce cycle times, and optimize workflows. Regular review of key performance indicators (KPIs) can also provide insights into areas that require improvement.
3. Cross-Training and Flexibility: Cross-training employees on multiple tasks and functions improves operational flexibility and reduces dependency on individual skill sets. Warehouse managers should provide opportunities for employee development and encourage cross-functional training. This ensures that the workforce is equipped to handle variations in demand, employee absences, or skill gaps.
4. Effective Communication: Clear and effective communication is crucial for smooth warehouse operations. Warehouse managers should establish open lines of communication with employees, suppliers, and customers. Regular team meetings, performance feedback sessions, and communication tools such as digital displays or messaging apps can facilitate effective communication.
5. Safety and Compliance: Safety should be a top priority in warehouse operations. Warehouse managers should implement safety protocols, provide proper training, and conduct regular safety audits. Compliance with local regulations and industry standards is also essential to avoid penalties and maintain a safe working environment.
6. Collaboration and Partnerships: Warehouse managers should foster collaboration with suppliers, customers, and other stakeholders in the supply chain. Close collaboration ensures timely deliveries, accurate order fulfillment, and efficient returns management. Building strong partnerships can also lead to improved negotiation power, cost savings, and enhanced customer satisfaction.
By adopting these best practices, warehouse managers can create a culture of continuous improvement, efficiency, and safety. Regular monitoring and evaluation of KPIs can provide valuable insights into the effectiveness of these practices and guide further improvements.
Training and Development for Warehouse Staff
Investing in the training and development of warehouse staff is crucial for building a skilled and motivated workforce. Well-trained employees not only perform their tasks more efficiently but also contribute to a positive work environment and improved overall productivity. Here are some key considerations for training and development in warehouse operations:
1. Initial Onboarding: When hiring new employees, warehouse managers should provide comprehensive onboarding programs to familiarize them with the warehouse environment, safety protocols, and key processes. This includes training on equipment operation, work procedures, and company policies. Onboarding programs should be tailored to the specific roles and responsibilities of each employee.
2. Skills Training: Warehouse managers should identify the specific skills required for each job function and provide targeted training programs. This can include forklift operation, inventory management software, order picking techniques